6 common points to note when assembling Anderson connectors
Anderson connectors, as key components for current or signal connections, are also an important component of industrial systems. From airplanes and rockets to electric vehicles, UPS power supplies, forklifts, chargers, lawn mowers, mobile power boards, and Anderson connectors, they all appear in various forms, serving as bridges between circuits or other components, and undertaking the role of current or signal connections. In the rapidly developing industrial process of informatization and electronicization, Anderson connectors play an increasingly important role due to their ability to simplify the assembly process of electronic products, improve the flexibility of design and production, and enhance the automation level of the entire system
& nbsp; The assembly process of Anderson industrial connector harnesses must be carried out very carefully, as any defects in the production assembly process can cause overall product failure, leading to accidents. Although manufacturers are aware of the severity, there are still some common mistakes made when producing and assembling wiring harnesses
6 common errors in the production and assembly process of Anderson connector harnesses
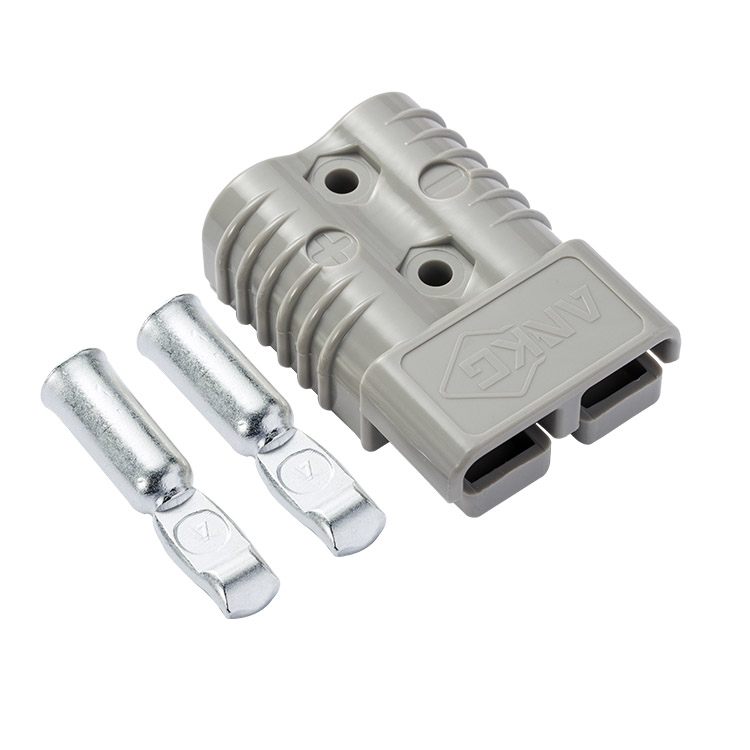
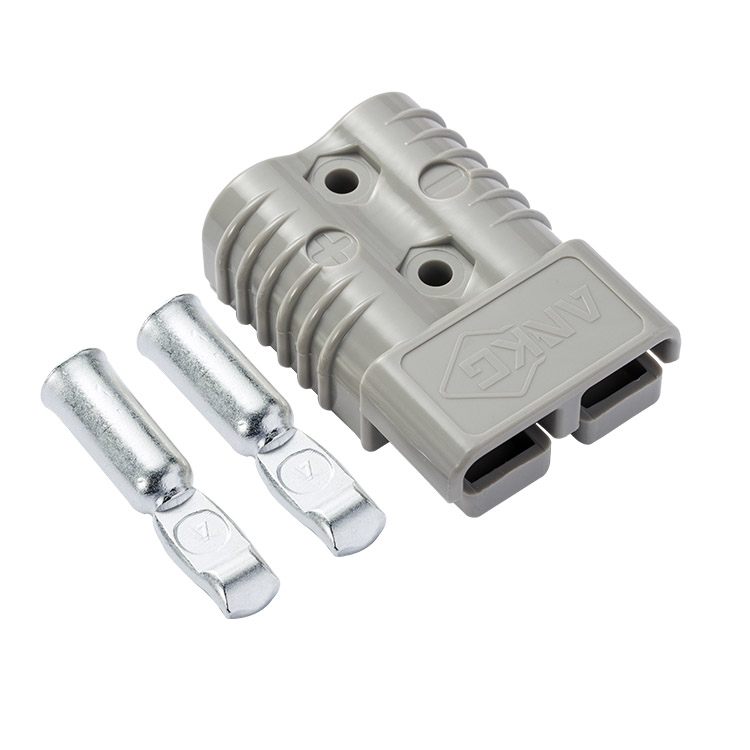
Anderson Industrial Connector Wire Harness
1. Prepare connectors and wires
The preparation of wires must be carried out with caution and precision, as it determines the overall efficiency and performance of the components. Many manufacturers make mistakes in this first stage by selecting the wrong wires, which are cut and stripped at the ends
2. Not following the assembly drawing
Not following the assembly diagram can lead to many problems when connecting wires in the chassis. Wiring harness manufacturers often make mistakes in connecting wires, which can cause wire components to fail and ultimately lead to system failure. It is necessary to strictly follow the assembly diagram to avoid such errors
3. Defects in crimping
The crimping process involves terminating the wire harness into the wire harness, which is the most critical step in the wire harness assembly. Improper execution can lead to open or short circuits. If many manufacturers randomly perform this operation, it can lead to product malfunctions
4. Incorrect Welding
Incorrect welding is another major area where manufacturers make mistakes. Improper welding of wires and terminals can cause thermal damage. When performing this operation, please use the correct welding equipment and welding temperature
5. Lack of wires and incorrect use of hardware
In order to meet the project schedule, some harness manufacturers may tend to overlook the crucial wires during assembly. This may cause malfunctions in the wiring harness components, and in addition, manufacturers may use incorrect hardware, including brackets, fixtures, washers, or screws, to assemble the wiring harness
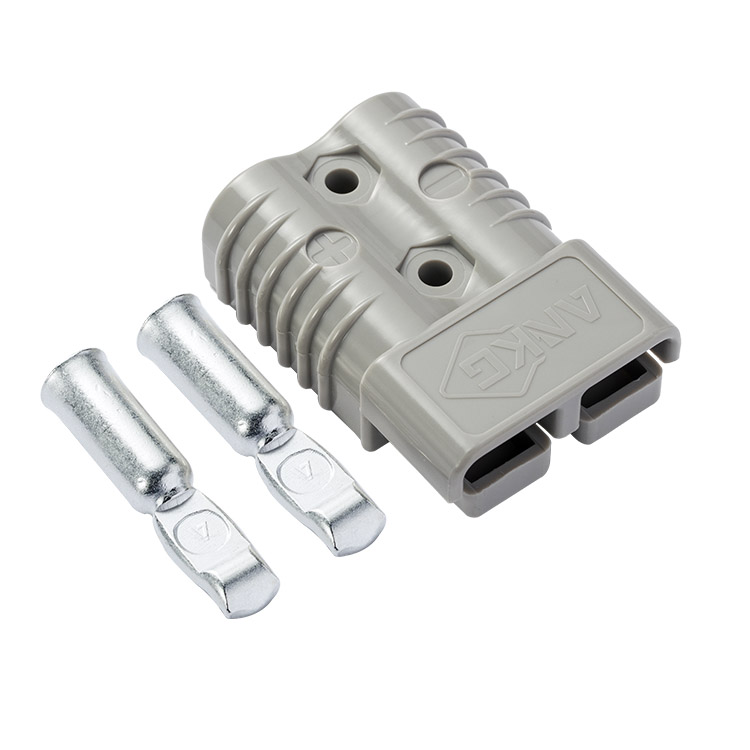
6. Incorrect wire connections
The final step in the wiring harness assembly process is to use plastic straps to tie the wires. Sometimes, the wiring harness manufacturer may wrap the wires too tightly, resulting in damage to the wires. On the other hand, if it is loose, it may not be possible to grip the bundle correctly, so manufacturers must ensure that the tie wraps are fastened around the wires in the correct way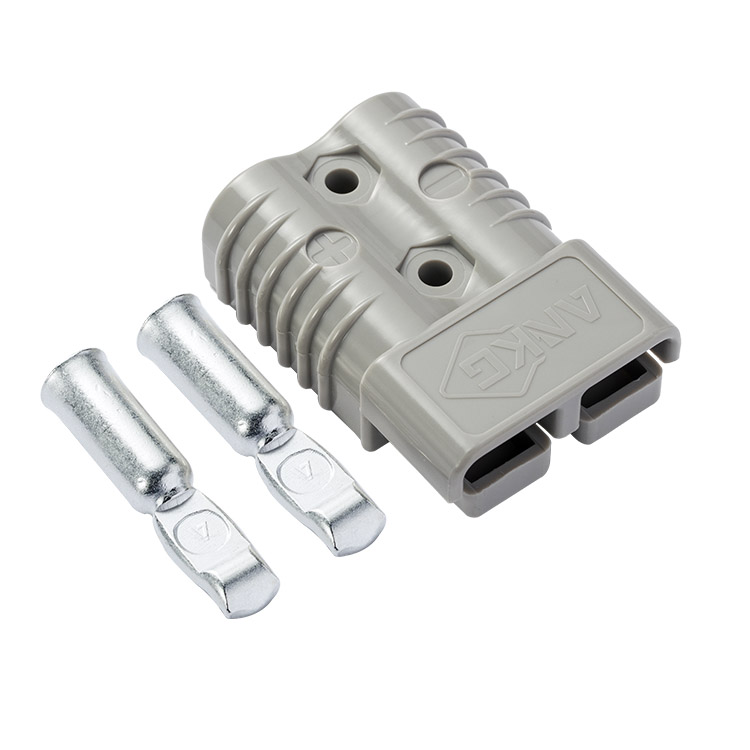
The Anderson high current connector market is experiencing a surge
At the same time, the demand for automation in smart factories will undoubtedly enable industrial robots to play more roles in the future. As an internal connection provider for robots, Anderson connector manufacturer, which provides sensing solutions, naturally cannot miss this promising sunrise field. The robotics industry is thriving in China, and the Anderson high current connector solution for local connections of robotic arms and complete and complete robot control systems is also attracting increasing interest. Although connectors are just a small component in the intelligent control process, they are the foundation for ensuring overall quality and achieving intelligence. The development of industrial robots will inevitably bring huge changes to the Anderson connector field, and this new development will also feed back to other fields of connectors, bringing revolutionary progress prospects to the entire connector device
With the shift of the world manufacturing industry to Chinese Mainland, the production focus of global connectors has also shifted to Chinese Mainland. China has become the largest connector production place in the world. The overall level of Anderson connector manufacturing in China has rapidly improved, and the market size of Anderson connectors has been expanding year by year. China has become the most promising and fastest-growing region in the global Anderson connector market
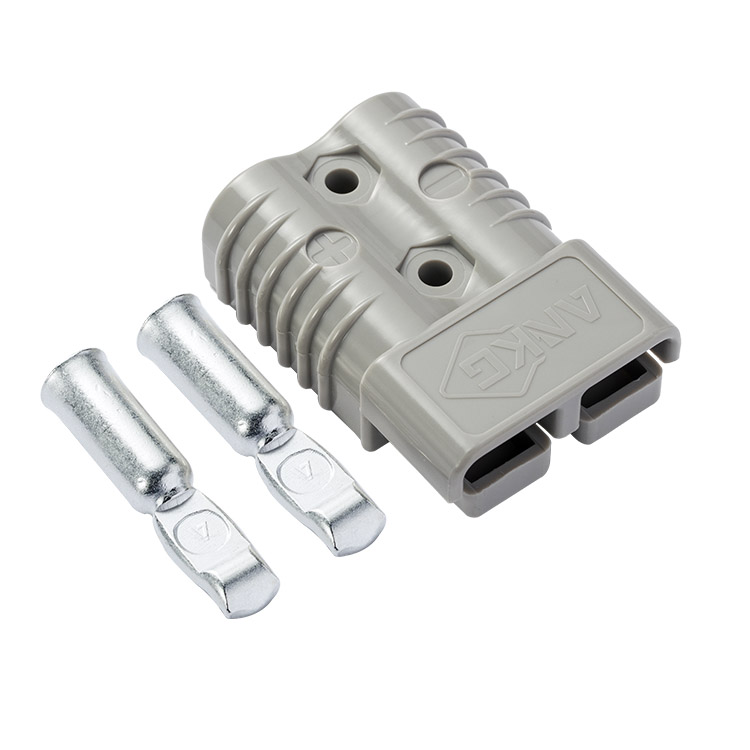
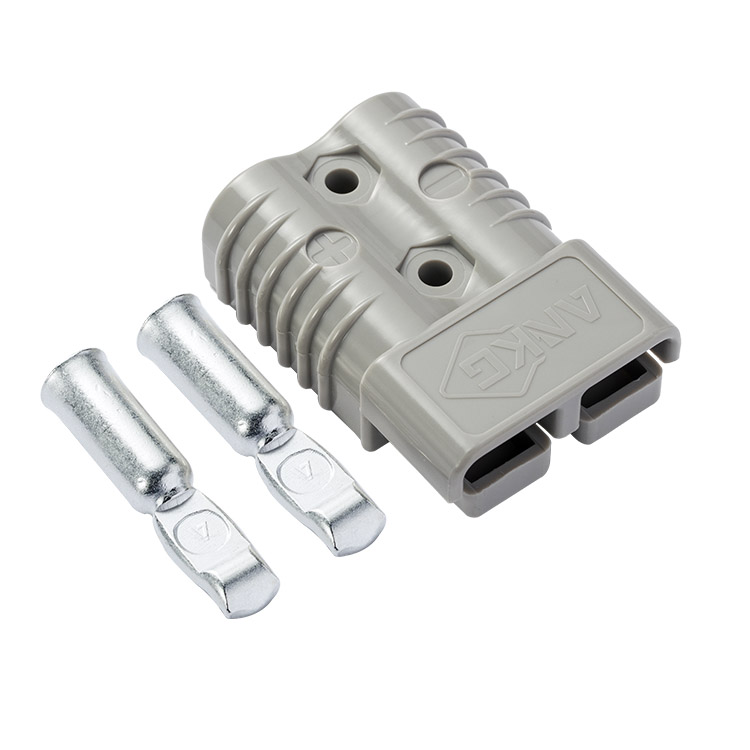